دایکاست (ریخته گری تحت فشار) چیست؟
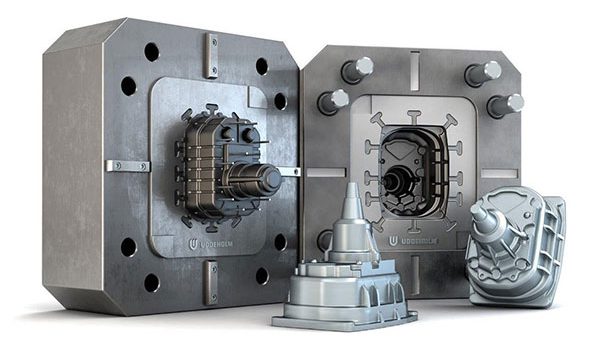
قالب دایکاست محفظه ی بستهای است که فلز مذاب تحت فشار و دمای بالا به داخل آن تزریق میشود سپس به سرعت خنک میشود تا قطعه جامد شده به اندازه کافی سفت و سخت شود و امکان خروج از قالب فراهم شود. این فرآیند با استفاده از تکنیک تولید محفظه سرد یا گرم که بر فشار بالا متکی است، فلز مذاب را با سرعت ۶۰ تا ۱۰۰ مایل (۹۶ تا ۱۶۰ کیلومتر) در ساعت به داخل قالب فولادی که قابل استفاده مجدد می یاشد تزریق میشود که در نهایت منجر به ساخت قالب دایکاست می گردد. در این روش، قطعاتی از طیف بادوام فلزات غیرآهنی مانند روی، منیزیم، آلومینیوم و مجموعهای از مواد کامپوزیت تولید میشود.
خطوط جداسازی قطعات و محصولات دایکاست
یکی از مهمترین پارامترهای طراحی قالبهای دایکاست تصمیمگیری در مورد نوعی از خط جدایی است که قطعه را شکافته و سطح تماس بین دو یا چند جزء را ایجاد میکند. جایی که طراح این خط را قرار میدهد به اشکال هندسی و میزان تحمل سطوح مختلف بستگی دارد. طراح دو انتخاب دارد یا یک خط جدایی مستقیم یا یک خط جدایی شکسته. باید سعی کنید قطعات را با خط جداکننده مستقیم طراحی کنید زیرا از نظر هزینه ابزار، کم هزینهترین گزینه است. هنگام تصمیمگیری در مورد خط جدایی، طراح باید عوامل زیر را در نظر بگیرد:
سفارش مشتری – معمولاً مشخصات قطعه یا محصول مشتری، قرار دادن خط جداسازی را به چالش میکشد. الزامات اجباری مشتری نیز به یک مسأله تبدیل میشود
برآورد هزینههای قالب – یک خط جداکننده مستقیم میتواند هزینه ابزارآلات را کاهش دهد. با این حال، در برخی موارد، طراحی یک خط جداکننده شکسته مقرون به صرفهتر خواهد بود زیرا در غیر این صورت ویژگیهایی که در قطعه مورد نظر وجود دارد شما را مجبور به راهاندازی خط جدیدی میکند که باعث یک هزینه سربار میباشد.
ماشینکاری و پرداخت – بیشتر قطعات نیاز به ماشینکاری پس از تولید دارند. قسمتهای از قطعه نیاز به کارهای تکمیلی و ماشین کاری دارند . ضمناً این قسمت نباید نیاز به زیبایی داشته باشد زیرا اثرات پرداختهای نهایی بر روی قطعه نمایان میشود.
جریان فلز مذاب – کیفیت تزریق فلز مذاب به محل مناسب ورودی قلب بستگی دارد. ورودی قالب باید روی خط جداکننده طراحی شود. این کار سه حسن دارد اول اینکه تعیین میکند که آیا قالب ریختهگری به درستی با فلز مذاب پر میشود. دوم تحت ریختهگری فشار بالا، مکانیزم تزریق یا پر کردن میتواند فلز را به درون ریختهگری فشار دهد تا از جمع شدن قطعه در طول انجماد جلوگیری کند و سوم اینکه با پرداخت خط جداکننده ورودی قالب نیز پرداخت شود
هستهها – موقعیت هستهها (هستهها سوراخهایی را در قطعه ایجاد میکنند) محل قرارگیری خط جداسازی را تعیین میکنند. طراح باید محل هسته و همچنین اندازه قطر و طول هر هسته را برای هر سوراخ مورد نیاز در ریختهگری در نظر بگیرد.
طی فرایند طراحی قالب دایکاست جریان مذاب از مهمترین ملاحظات میباشد. اگر قالب به دقت پر نشود منجر به نقصهایی در قطعه خروجی میشود این نقصها به شکل خطوط سطحی و یا حفرههای هوا به صورت مک داخلی بر روی قطعه نمایان میشود که باعث کاهش استحکام و زیبایی قطعه میشود.
همچنین طراح باید پران ها را که قطعه را از قالب خارج میکند در طراحی خود مورد توجه قرار دهد. پران ها باید طوری طراحی شوند که حداقل علائم را بر روی قطعه برجا بگذارند. یکی از حسنهای پران جلوگیری از خم شدن قطعه میباشد. اثرات پین پران بر روی قطعات به صورت فشرده یا برجسته در حدود 0.3 میلیمتر میباشد. قطر نشانههای پین پران بسته به اندازه ریختهگری متفاوت خواهد بود.